AI is disrupting education. But despite what the headlines (and some ChatGPT horror stories) might suggest, South African teachers aren’t being replaced — they’re…
Digitisation: ‘You don’t need robots and drones to benefit’
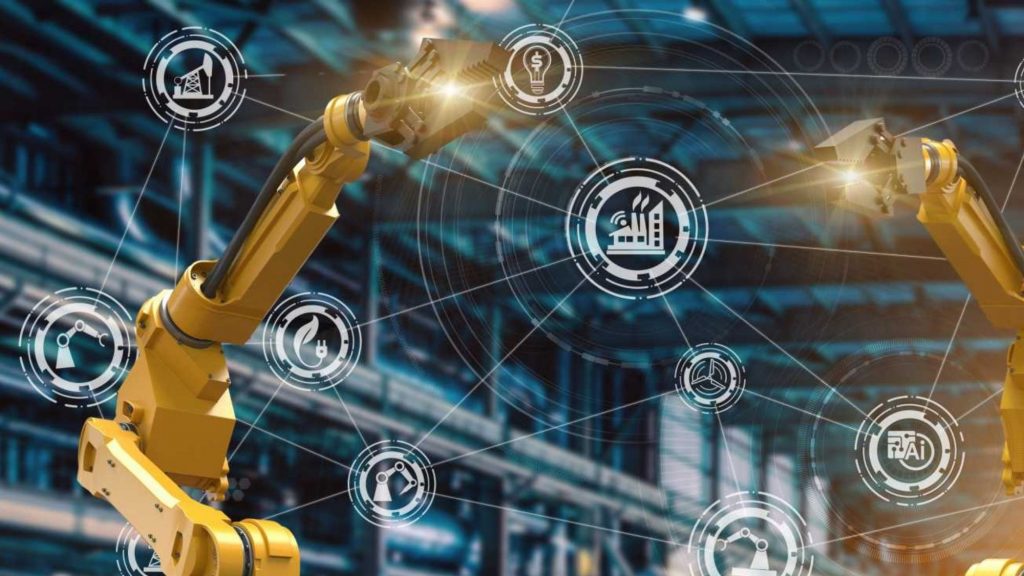
The march of digitisation across manufacturing and engineering start-ups continues. While this is not breaking news, QuickEasy BOS ERP commercial director Anton Oosthuizen is concerned that many entrepreneurs aren’t clear on exactly how they can embrace this in the workplace. Nor is there much clarity on the knock-on effect it might have to other areas.
According to Joe Terino, a partner at Bain & Company, “Digitisation will have the impact on supply chains that steam and electricity had on manufacturing.”
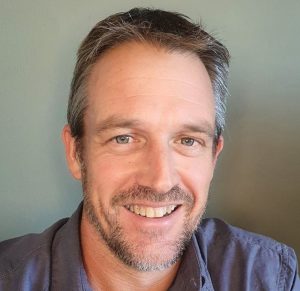
A bold statement, and yet to reach its fullest fruition. Nearly 30 years after the emergence of the internet as a business tool, and supply chain management most multinational corporations are still surprisingly backward-looking and – dare I say it – sluggish.
Many organisations are burdened with legacy, outdated systems that were custom-built decades ago, and simply cannot keep up with the pace and demand of modern industry.
According to a Parsable study released in March 2021, 79% of factory workers still rely on paper-based documentation and checklists to track work and communicate with their team.
We’re talking multi-million-dollar enterprises that still work with spreadsheets, paper, and siloed or patchwork systems that do not communicate with each other.
Herein lies the rub. This is a house of cards waiting to collapse. Manual systems do the opposite of what they are meant to do. Instead of helping you build a profitable business, they could be your biggest stumbling block.
Here are some of the challenges paper-based systems create.
Lack of data security and privacy
It is important for every organisation to protect its data and other information assets, regardless of its size. Businesses face a number of information security risks with paper documents because they can be easily lost, damaged or mishandled, whereas digital data can be encrypted and safely stored in the cloud or on firewall-protected servers.
Susceptible to damage and loss
It is easy to lose documents, which results in a delay in payment, or worse, a claim against you for lost goods.
In the event of a fire or natural disaster, crucial information could be lost because manual documents can easily be damaged, lost, misplaced, or stolen. Once the paper documents are gone, there is no way of getting that data back.
Document transportation
Transporting documents in a paper-based system is bulky, complicated, slow, prone to loss, and inefficient. When digitised, you simply create your document, download it in digital format, scan and interact with it, add attachments to an email, or upload to the server, and send information instantly.
Limited editing and version control
Making changes to paper-based documents means you need to re-write the entire document or have multiple versions of the document floating around the business. This exposes the company to risk, fraud, mismanagement, and poor customer experiences.
Admin and productivity costs
The direct and indirect costs associated with paper-based processes and systems are one of its biggest drawbacks. Aside from the paper, printers, stationery, storage, and office supply costs, the hefty costs of bloated admin teams required to manage this is often the biggest expense. Not to mention the unrecoverable hours of productivity that are lost to manual admin, data capture, human errors, reporting, and invoicing.
Fractured communication and collaboration
It is extremely difficult for teams to collaborate within a paper-based environment. I’m talking about multi-department collaboration that is stifled due to non-communicative systems. Don’t even mention how restrictive and frustrating this is for multinational teams. Digitisation of processes and admin allows employees to collaborate faster and easier, while increasing accountability, transparency, productivity, and tracking changes automatically.
Digitising distribution and delivery
It is because of these challenges that manufacturing, and enterprise leaders are so gung-ho about digitisation.
In fact, a recent study published by Zebra Technologies stated that manufacturers across EMEA aim to ramp up the introduction of new technologies in the coming year. All of this in a bid to bring goods to market faster (43%), to address the ever-growing supply chain complexities (41%) and to enhance connectivity throughout their business (40%).
A variety of new technologies and methods are being experimented with in many industries that promise to improve how they plan, source, make, and deliver their products. As a result of these innovations, supply chains are becoming more predictable, transparent, and efficient.
The good news? You don’t need to roll out bleeding-edge technologies, robots, and drone fleets to reap the benefits of digitisation.
Today’s manufacturers and distributors can leverage advances in technology and cherry-pick the tried-and-tested developments that have proven beneficial, and more importantly, are stable! Integrated warehousing management applications such as business operating systems that talk to mobile scanning devices, inventory management, advanced analytics, and automated accounting are all within grasp for any distributor keen to take advantage of digitisation.
The value difference
As that industry transforms itself, digital distribution has become its moniker. There is a transition underway in distribution as the industry, consumers, and products we move become more digital.
Digital distribution contributes value by enabling capabilities like same-day delivery or seamless return of faulty products. In other words, automation of several cogs of the supply chain ultimately offers value and brings return. Things like reducing errors in warehouses through mobile scanners, speeding up employee tasks through business tools, and saving customers’ and back-office staff’s time through digital delivery notes.
This is where enterprise resource planning (ERP) software makes one manufacturer stand apart from the rest. ERP is not a new technology in the manufacturing space. They’ve been using it for decades. Modern ERP, however, is what separates the sheep from the goats.
Agile, scalable, customisable, and fast as you please, it brings the entire business – front and back office and manufacturing – under one roof.
Plus, once you start feeding data into analytics, it unlocks a whole new world of planning and prediction. New services for customers are developed, including real-time supply chains and just-in-time (JIT) stock management.
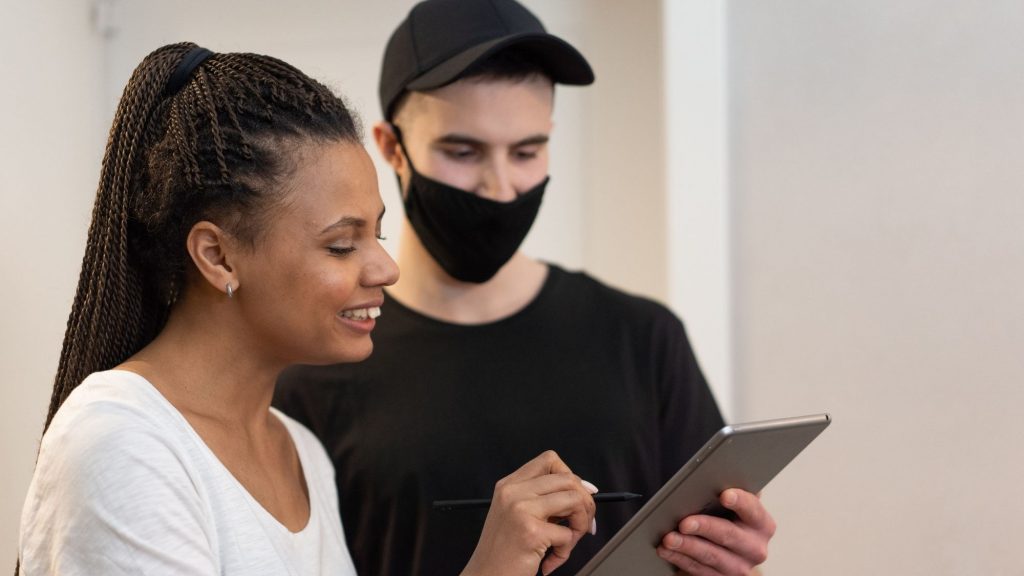
Paperless delivery integrated with ERP
The delivery note is of supreme importance. It is laden with crucial information, such as product number, invoice number, receiver, and sender names and, most importantly, the signature or proof of receipt.
For this reason, many companies have switched to digital delivery notes and gone paperless. This is not new. What is new is that digital delivery notes are integrated with ERP. At QuickEasy, we’ve been doing digital delivery notes for a while, and have brought amazing functionality to thousands of users around the world.
Here’s how it works. First, the paperless process from quotation to work orders and manufacturing is all integrated in one BOS ERP system. This means, all those paper-based challenges mentioned earlier are eliminated, staff are productive, products are traceable, and production deadlines are met.
Once the product is ready for delivery, your ERP should automatically do the following:
- Create and order delivery batches.
- Customer and product details are automatically present on the delivery note.
- Drivers know exactly where to go and who to contact.
- Items are easily tracked, and status is updated to ‘in transit’ in the system.
- The customer signs the digital delivery note on a connected tablet.
- Status is automatically changed to ‘delivered’.
- You can email the delivery note directly to the buyer with one click, or you can set it to automatically send email confirmation that delivery is complete.
- The signed document serves as proof to avoid claims.
- Accounting can process the invoice as soon as they receive notification.
- Digital delivery notes can also be added to the invoice as proof.
- You can download the electronic delivery note in other digital formats, such as PDF, Word, or Excel.
No paper, no lost documents, no fractured communication, no risk. Digitisation at its most practical, most achievable form.
In spite of the opportunities and benefits of digitisation through ERP and electronic delivery notes, some distributors still resist change. The reason I have found is that digitisation is not just about new technology; it is about shifting mindsets and updating processes. This can feel unsafe and unfamiliar.
There is no doubt that some products are run-rate and volume-driven, and focussed on breadth, whereas others require the distributor and reseller’s commitment. This type of digitisation needs more than technology. It requires an experienced implementation partner who understands your industry, who can offer advice and support to navigate around difficult areas, as well as provide technology solutions.
Digitalisation benefits manufacturers and distributors greatly and this sector is home to some of the most cutting-edge innovations. Thankfully, you don’t have to deploy AI-powered robots to leverage those benefits. You can simply start by speaking to experts in the industry who have the know how to help you deliver digitally.
- Anton Oosthuizen is the commercial director for QuickEasy BOS ERP in South Africa.
ALSO READ: Five trends that predict the future of manufacturing